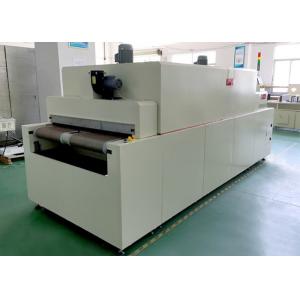
Add to Cart
Infrared Tunnel Baking Furnace
Function: The equipment is suitable for drying after printing ink on composite board and acrylic surface.
Equipment specifications and main technical indicators.
1. Use beige Teflon cloth conveyor net, net width 600mm
2. Automatic deviation correction is used to prevent deviation of the conveying net.
3. Adopt frequency converter to freely adjust the stepless speed, the speed range is 0.5-5m/min.
4. High-grade fully enclosed gear reducer motor drive.
5. Three-layer independent conveying mechanism, back-and-forth conveying.
Blanking method between layers
1. Use the roller pallet to cut the material, the third layer of material comes out and enters the blanking roller to the pallet, the pallet returns the product to the second layer for baking, and the second layer of material comes out into the blanking roller to the pallet , The pallet is returned and the product falls into the first layer for baking.
Structure distribution
1. External dimensions: L9000mm×W1500mm×H2150mm
2. Feeding section: 1500mm
3. Heating section: 5000mm (Equally divided into 3 sections, 3 layers of heating sections total 15000mm)
4. Cooling section: 500mm
5. Discharge section: 500mm
6. Material transfer layer: 1500mm
7. The conveyor net is above the ground: 1000mm
Furnace body material:
1. The exterior is made of steel plate with high temperature paint after anti-rust treatment, and the sheet metal sealing plate around the base
2. SUS201#1.5t mirror stainless steel plate is used inside.
protective device:
1. In addition to the main temperature control and the upper and lower limit over temperature prevention circuit, the over temperature protection is also equipped with a secondary temperature control
The over-temperature preventer is the safest temperature protector. When the over-temperature temperature is abnormal, the alarm will sound and the power will be automatically cut off.
Source system to prevent accidents.
2. The drive motor is equipped with reverse phase protection to prevent the motor from being too high after reverse phase, causing product defects and equipment damage.
3. Equipped with an emergency stop switch, each heating section circuit overcurrent, overload protection and interlocking.
4. When an abnormality occurs, the abnormal indicator and buzzer alarm are used to facilitate the operator to eliminate the abnormality.